Water treatment for the food industry
In the food industry water must meet at least the quality indicators prescribed in SanPiN 2.2.4-171-10 (or the old GOST "Drinking Water").
Order cleaning
This applies to all businesses, from the production of pasta and dairy products to the production of bottled water. However, in each specific area and in the peculiarities of the technological process, there are peculiarities in terms of certain chemical parameters. So water is used as a technological raw material, for the use of personnel or for chemical water treatment for the boiler room. Specialists of our company will take into account all points of water intake and offer a distributed water treatment system, the design of which is guided by the following: the analysis of raw water, the experience of technologists and regulatory documents. Based on the correctly set TOR, the company "Akvarum" can offer:
- modernization of outdated treatment systems
- service maintenance of existing systems
- Design, installation and adjustment of new water treatment systems
The food industry applies the whole range of continuous and batch water treatment equipment from mechanical filters to desalting plants and ultrafiltration membrane disinfection installations:
- Cartridge filters for small systems
- Continuous and batch softening units with water flow regeneration
- Installations with ion exchange resins of different actions
- Iron, manganese and hydrogen sulphide removal units
- Industrial and household reverse osmosis units for water demineralization
- Dosing stations - acidification, alkalization
- Ultrafiltration disinfection units
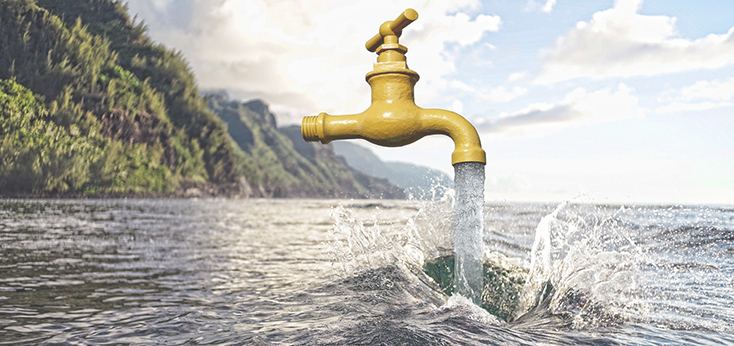
Untreated tap water contains mechanical impurities, metals, bacteria, pesticides, chemicals in varying amounts that accumulate in the body and can cause various diseases.

Water treatment helps get rid of the unpleasant taste and odor that appear as a result of an increase in the concentration of inorganic and organic substances in the composition of such water.
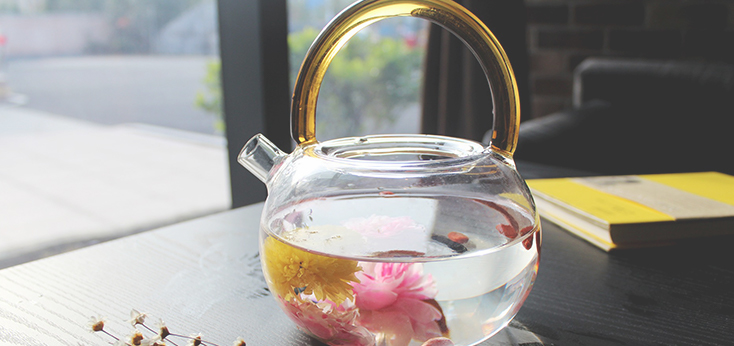
Lithuanian water leads to the accumulation of scale on the heating surfaces of electrical appliances, consequently reducing their thermal conductivity. This accelerates appliance failure and increases energy costs.
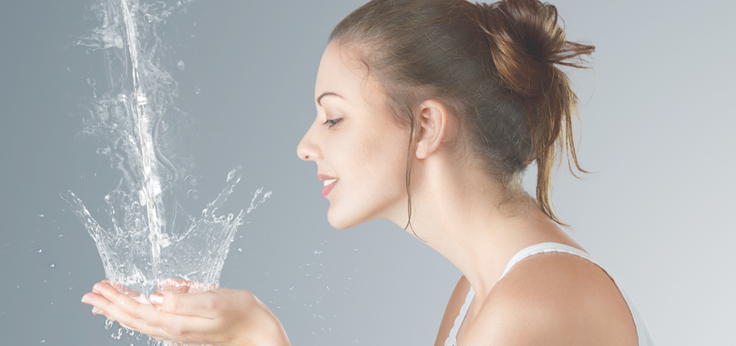
It is known that the consumption of clean water is extremely important for maintaining health. That is why purified water is necessary for a person to protect himself from many diseases and to continue an active life without doctors and pills.
All equipment is certified by the State Sanitary and Epidemiological Service of Ukraine.
To get a consultation or a commercial offer for water treatment in the food industry fill out the form and we will contact you within 15 minutes.
Milk production
In milk production, water is used for the following
- disinfection of equipment and tanks;
- room cleaning;
- product washing;
- reconstitution of milk;
- cooling.
For different needs from 2 to 5 liters of water per 1 liter of milk is consumed.
Sugar and sugar refineries
1. Processing of sugar beet.
Figure 1 shows a simplified diagram of sugar beet processing
sugar beet processing. Industrial water treatment technologies are used to purify the sub-
beet water and the juice itself. As consumers of large volumes of
Sugar factories have been gradually reducing their water consumption by installing
internal water recycling and reuse systems:
Figure 1: Water cycle in a sugar beet processing plant. Balance in m3 per 100 tons of sugar beet
Source: Technical Handbook for Water Treatment: in 2 vols., Vol. 1: transl. from Fr. - St. Petersburg: New Journal, 2007
- Sugar beet washing: a turnover of contaminated water through a sedimentation tank with a
scraper;
- soaking beet chips (making raw juice): treatment of condensed ammonia water for reuse in soaking;
- treatment of the diluted solution:
- Decalcification of liquor after second carbonate treatment (to protect
decalcification of a solution after a second carbonate treatment (to protect evaporation equipment against scaling);
- Demineralization of the solution (reduced molasses yield);
- Decolorization of molasses on activated carbon or adsorbing resins;
- Thickening of the solution, sugar crystallization by means of juice concentration in evaporators;
- Waste treatment (effluent or molasses) to reduce sugar molasses yield
sugar molasses yields and to reduce sugar losses:
- Treatment of effluent on cation-exchange resin charged with magnesium chloride
(Quentin process); replacement of Na and K ions with Md
in the molasses;
- Demineralization of effluent and molasses on ion exchangers (with additional purification if necessary) to obtain a sugar solution;
- water make-up:
- pouring into boilers at the beginning of the beet processing season or when there is an unexpected
Water top-up: Filling up the boilers at the beginning of the beet processing season or an unexpected shortage of returnable condensate;
- Continuous supply of water for the cooling systems of turbine generators and for the primary treatment of the sugar beet.
Since sugar beets have an average water content of 77 %, a sugar factory
The sugar beet plant generates a surplus of water (see Fig. 1).
Note that of the 28 m3 of excess water, in fact 10 m3 is returned to the sugar beet washing, 8 m3 is used for other flushing and make-up of the boilers, and only 10 m3 is returned to the sugar mill.
only 10 m3 is returned to the environment.
2. Sugar cane processing
The purification of the original sugar cane juice requires the use of
Clarification techniques similar to those used in water treatment:
- accelerated sedimentation of juice clarified with lime;
- Flotation of the clarified juice in order to separate the empty bagasse;
- disinfection of the water circulation circuits (mandatory).
3. Refining of sugar (beet or cane)
Supersaturated syrups and sugar solutions must be treated for more or less complete discoloration.
4. Canned fruits and vegetables
On average the production of 1 ton of canned fruit and vegetables requires 40 m3
m3 of water is required for the production of 1 tonne of preserved fruit and vegetables.
Production water usually requires softening, at least
partial softening. But reducing the total salt content can be useful for
Prevent corrosion of canning jars.
own enterprise
customized solutions
operational experience
and installation
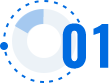
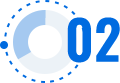
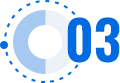
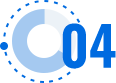
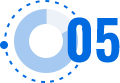
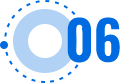